Fort Hood Texas
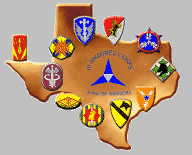
M-113 Cooling fan
angle drive
Scope of this report
This report details testing performed at Fort Hood , Texas during May and June
1983 on the cooling fan assembly of the M-113 Armoured Personnel Carrier and
related series vehicles.
Situation
The cooling fan assembly in these vehicles
experiences higher failure rates than would seem normal for such a mechanical
assembly. This led to a disproportionate recurrence of Not Mission Capable
(NMC) ratings from failure.
Test objective
The objective of the test is basically two - fold. First to determine if the
currently used lubricant was sufficient for this application, and secondly, to
determine the feasibility of a lubricant which provided a wide S.A.E. range
coupled with a bonded dry - film lubricant.
Test methodology
The fans were driven by a seven and one - half ( 7 1/2 ) electric motor on each
fan assembly, through a pulley and belt arrangement. The motors provided 1760
r.p.m. fixed speed.
In phase 1, ratios were set to produce fan r.p.m.'s of 3461; and in phase 2
ratios were set to produce fan r.p.m.'s of 4,861.
First phase of test to last @ 50 hours with second phase of testing to last an
additional 50 hours , for a total of 100 hours running time.
This is an acceptable procedure and was patterned
after the Federal Aviation Administration test procedures for lubrication
certification and type acceptance.
Unit #1
was a salvage M-113 A 2 cooling fan repaired and assembled by L.V. Cammack and inspected and certified as being in compliance with the
specifications and tolerances of TM 9 - 2520 - 238 -34. C2. by Charles
Taylor and Jack Peebles.
It was lubricated
with XcelPlus Formula 844.
Unit #2
was a new issue unit from D.I.O., inspected and certified by ;
Jack Peebles. This unit was lubricated with
MIL -L-21260, Grade 2, SAE 30 drawn from stock.
Variances
During assembly of Unit # 1, it was discovered
that the gear housing around needle bearing 20 was scarred. This was filed and
emery clothed, cleaned and blown dried. Both Input / Output gears were shimmed
to minimize backlash.
Test run 1 - 6
First run lasted 8 minutes and 30 seconds at which time both fuses blew. During
this time both units seemed to function normally.
Unit # 1 had a pronounced vibration which
could be felt in the dust cover and had a low frequency noise of an undetermined
nature.
Test run # 7
Units are displaying great differences. Test carried through 34 : 04 : 27 for
this run differences noted as follows:
09:57:32 fuses failed Unit #1 bearing slightly warm Housing slightly
warm. Unit # 2 housing very warm, input shaft was slightly hot. A grinding noise
could be detected in
Unit # 2 with a
stethoscope, coast down time 7 seconds shorter than Unit # 1.
28:12:00
Unit # 2 had a loud whine that
lasted about a minute then disappeared. It sounded like some sort of metal to
metal contact was taking place. Unit #
1 still had a slight whine.
30:30:00 Both units stopped for inspection. a new noise could be heard in
Unit # 2 coast down time @ 10 seconds shorter than Unit #1.
Unit # 2 housing was warm with input shaft
being hot. Unit # 1 remained slightly
warm to warm on all surfaces.
32:37:43 A new loud grinding noise was heard from Unit #2 for about 15
seconds. Stethoscopic inspection determined this noise to be coming from the
gears.
34:04:27
A loud grinding noise developed
in Unit #2 both units stopped for inspection. Coast down time for Unit #
2 @ 15 seconds shorter than Unit #1.
Unit #1
had no surface temperature greater than slightly warm.
Unit #2 Upper housing very warm, Lower housing slightly hot. Shaft and
inner bearing very hot.
Testing of unit # 2 was therefore terminated.
Unit # 1 was
operating in a normal manner.
Test run 8 - 10
Unit # 1 was run for 12:48:20 with no
remarkable notations. None of the surfaces were greater than warm. No unusual
noises heard.
It was decided both units should be run at a
higher r.p.m.'s in order to push at least one of the units to some degree of
self destruction.
Unit #1 was run at 4861 rpm for 14:43:15 to
see if it could be knocked out of service as well. During the run there were no
remarkable notations. Unit only ran slightly warm to warm.
Both units were run side by side.
Unit #1
performed normally and ran no greater temperatures than warm.
Unit #2 initially performed normally, due to
it's ability to have cooled down. However soon began making a noticeable
grinding noise during the end of the run. Temperatures for the housing were
warm and very warm with the shaft being very hot.
Test run 14
Test was
terminated at this point. Total time for both units at elevated rpm's
22:56:22. It was determined in the interest of safety the tests be terminated.
Unit #2 housing surfaces were very hot with
shaft being very hot. There was also a grinding noise in frequency noted
during the run which was the determining factor to terminate the tests.
Unit #1 performed normally with surface
temperatures only running slightly warm.
Post test inspection
All components of Unit #1 were found
to be serviceable with no indication of wear nor deterioration. Oil Unit #1 was
clean and manifested no signs of deterioration.
In the inspection of Unit #2 the first feature to be noticed was the scoring of
the inner diameter of the fan tower. It was this scoring that lead to the
cessation of the testing. disassembly showed greater bearing failure that
had been suspected. Oil from Unit #2 appeared to have sustained some
degree of burning.
All
internal parts were sent to N.A.S.A. labs for detailed inspection.
Testing at NASA proved the coating to be 1
micron thick and bonded to the metal surfaces. The tests were performed
with NASA's electron Microscope and proved the dry-film lubricant had rebonded
only to the bare metal surfaces and not to itself. NASA photos are included in
this summary.
Recommendation
It is recommended that the Angle Drive Fan Assemblies of the M-113 and related
series vehicles be treated with XcelPlus Formula and that they only be run with
this lubricant installed.
Temperature scale
explanation
Slightly warm: |
A slight temperature elevation can be noted but is minor |
Warm: |
Temperature elevation is very apparent but does not cause discomfort if
held |
Very warm: |
Causes discomfort if held but does not cause pain |
Slightly
hot: |
Causes discomfort and pain if held to skin discoloration |
Hot: |
Pain if held, prolonged contact results in minor skin discoloration |
Very hot: |
Causes pain and skin discoloration if touched |
Extremely
hot: |
Causes pain and blistering if touched |
Duration of tests run
Run # |
Total hours run |
|
Unit # 1 |
Unit # 2 |
1-3 |
00:30:51 |
00:30:51 |
4-6 |
03:44:25 |
03:44:25 |
7-9 |
65:20:27 |
37:48:52 |
10-12 |
75:55:27 |
54:33:07 |
13-14 |
82:17:34 |
61:15:14 |
Run
# 1 thru Run # 8 were made with input RPM of 3,641
Run # 9 thru Run # 14 were made with input RPM of 4,861
 |
Inner race from treated bearing
(fig 3)
The surface coated with XcelPlus and although the coverage is not
complete, the picture shows conclusive evidence of the protection
afforded the surface and
that the bonding has withstood a considerable amount of extreme friction.
For all practical purposes, this surface can be considered "brand
new". It becomes more dramatic when compared with the untreated
surface below, and it is remembered that both surfaces were sustaining
identical amounts of use.
This race is apparently capable of sustained operation and would still
be serviceable. |
 |
Race from
untreated unit (fig 4)
This photo
shows the results of the ball in Fig. 2 skidding across the surface.
This is the classic example of galling of a race by a ball due to
inadequate lubrication. Close examination shows that the metal is being
"peeled" as well as scored. Pitting is also occurring.
It was this wear which allowed the impeller to develop the horizontal
movement which resulted in the scoring of the inner diameter of the fan
tower. |
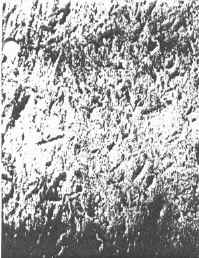 |
Ball bearing from treated unit
(fig 1)
This surface shows
signs of almost total coating with XcelPlus and
virtually no wear or deterioration.
There is no indication of skid, smearing, brineeling, nor spalling.
This ball surface is only slightly different from a new ball. |
 |
Ball bearing for
untreated unit
(fig 2)
This ball surface
shows considerable wear. There is evidence of primary brineeling,
skidding and spalling.
In spite of the fact that the ball wears the least (in comparison with
the race) this ball does show that it is wearing.
Wear of this
nature is generally the result of inadequate lubrication. It is
discussed in more detail in the evaluation of this report. |
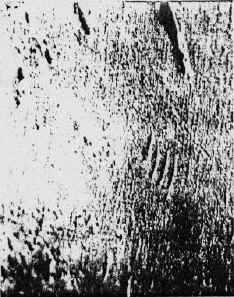 |
Gear in treated
unit
(fig. 5)
This gear is virtually without wear. Were it not for the coating of
film it could be brand new.
The marks left by milling prove conclusively that the bonding agent does
not rebond to itself.
The one (1) micron thick coating
has not filled the holes left by the milling process, but the coverage
is almost total.
This dry - film lubricant
was responsible for the extraordinary temperature drop in the treated
unit.
The fluid
lubricant has fulfilled its job in this unit and the dry film of XcelPlus
has reduced friction and wear |
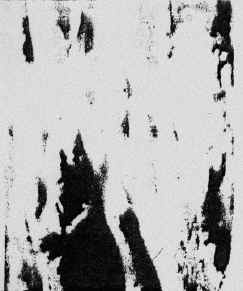 |
Gear in untreated
unit (fig 6)
The gear surface
sustained considerable wear and deterioration. Galling has occurred and
brineeling also.
The flaking of metal can be seen and in the lower left hand corner,
and actual flake can be seen.
The temperature has been exceedingly high, as evidenced by the
bubbling effect.
Wear of this nature is almost always a result of inadequate
lubrication. It can result in a syndrome wherein the surface is worn,
then that wear defeats the formation of the oil wedge which creates
higher heating which defeats the oil wedge, etc... |
|
Photos 2000X - NASA Pasadena, Texas |
|